I have been involved with hundreds of projects in one capacity or another where I’ve designed or commissioned HVAC systems. With only a few exceptions, it’s been my experience that ductwork is never installed exactly as drawn. Most of the time it’s close. Usually, this is due to a lack of coordination during design requiring in-field modifications or a lack of detail when it comes to equipment hookups. We all expect design engineers to have their designs perfectly coordinated and their equipment details to be exact. I was on the design side for more than 10 years and I can tell you that there is never enough fee or enough time in the design schedule for that to be a reality. Until that changes, we’d all better expect field modifications.
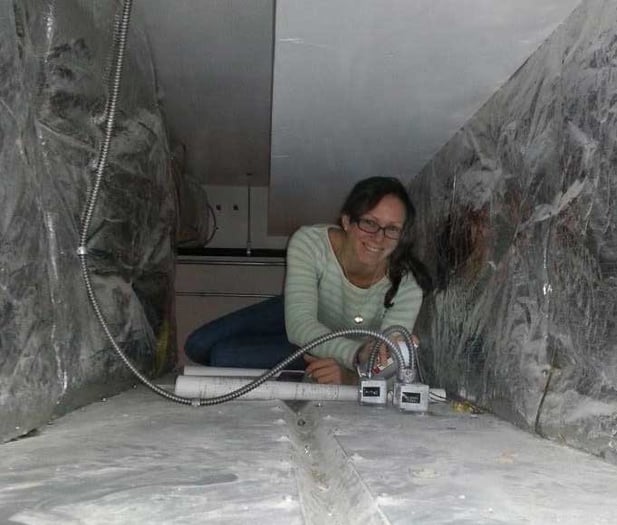
Design vs. Installation
That being the case, we as commissioning providers have to pay close attention to the implications of those modifications. We typically spend a lot more time in the field than the designers (their budgets are shot by now, remember?) and so we have more opportunity to look for and identify the changes. Sheet metal contractors are experts at installing sheet metal, not designing it. They are great at making things fit but aren’t always familiar with how they’ve affected the system when they make changes. Almost all the time, these changes are made to get the ductwork to fit. Doing so adds elbows, offsets and odd transitions, all of which add pressure drop to the system. The installation happens once but the duct system will be in place for 20, 30 maybe even 40 years before it’s renovated. That’s a lot of hours of operation over which the additional energy required to overcome the added pressure loss can add up.
Modifications Over Time
Another thing to consider is how the system will be modified over time. While we can’t predict the future, we can minimize the impacts of future changes. One example is a hospital central air handler that we recently overhauled. The unit was built in the early 1980s and there were some less-than-ideal main duct transitions and connections to the AHU plenum installed. At the time, the ducts were all properly sized for the expected service and the additional pressure loss was reasonably low; I’d estimate something like 0.25 to 0.33 additional inches of pressure. Consider that this is a 200,000 CFM system and you can realize that that additional pressure amounts to about 13 kW of additional operating energy or over 113 MWh of energy (costing $13,500) per year (being a hospital it operates 24/7). That was in the early 1980’s. Over time, the various spaces in the hospital have been renovated and upgraded to modern standards and this adds load from equipment and increases airflow requirements to maintain higher air change rates.
Fast forward to today. Those fittings I mentioned earlier are now supporting a fair bit more airflow than they were designed for. A balancing contractor recently measured the pressure drop across two of these fittings, which happen to be in series, and found the loss to be just over 1.3 inches! OUCH! That means over 445 MWh of wasted energy (or $53,000!) every year.
Often, we make small changes without considering the long term, potential impacts. Simple adjustments during construction, often with little or no first cost increase, can be made to limit or eliminate those lasting, long term impacts.
(Note – the pressure drop and MWh increases are, in fact, proportional in this case because while this particular zone has been overloaded, others have had their loads reduced and the unit CFM has remained roughly constant.)
