Building controls are always the last thing to get done on a project – at least on the mechanical side. They basically have to be. You can’t control what isn’t there and until the systems and equipment have been fully installed, started and balanced, the controls contractor can’t finish. As a result, controls contractors are often rushed and expected to complete, say, two weeks of work in two days. The result is often less-than-complete controls or a system that hasn’t been fully vetted which, sooner or later, results in a confused or unhappy building owner or occupants.
The thing about controls is you can’t see them. Sure, you can see the thermostat or the CO2 sensor, and you can even go one level deeper and find the controllers, but you typically don’t see “the man behind the curtain” – the programming, the nuts and bolts, or more accurately, the ones and zeros that make it all work. When a cooling tower is supposed to be there, but it isn’t, even an apprentice carpenter can tell something is amiss because there’s this box drawn on a blueprint that isn’t there in real life. Not so with controls. Following up on Ben Fowler’s recent blog post on common pitfalls often encountered with building controls system graphics, the following are three other issues with building controls we recently discovered that could have had significant consequences had they not been corrected.
Backwards Economizer
When reviewing the controls programming for a large central air handler, we began testing the differential enthalpy economizer. The programmer had included logic for this portion of the sequence of operation, but we found the differential part was backwards. The programmer enabled the economizer when the outside air enthalpy was higher and not lower than the return air. The engineer’s sequences said something like “use economizer when conditions are favorable.” The programmer was relatively inexperienced and didn’t even know what enthalpy was (his degree was actually in computer programming). We corrected this in less than five minutes, but had we not caught the error, the air handler would have used much more energy for cooling than necessary and under some conditions and the building would have been uncomfortable due to high temperatures and humidity levels.
The Boiler Alarm that Wasn’t
Recently, as part of a boiler functional test, we simulated a boiler failure by closing the gas valve and preventing the boiler from firing. The boiler went into alarm, but the BMS didn’t recognize that alarm and didn’t report it. The contractor had simply picked up the wrong contact on the boiler controller and this was fixed in about 15 minutes after some rewiring and reprogramming. This contractor had the good sense to add a low hot water supply temperature alarm to the system as a backup (even though it wasn’t called for) so eventually the building operator would have been alerted to the fact that there was an issue. But since the alarm wasn’t wired through the BMS, the operator wouldn’t have known the boiler was in alarm until physically walking up to it. Had the contractor not included the additional low water temperature alarm, this could have been disastrous if the boiler failed in the middle of winter.
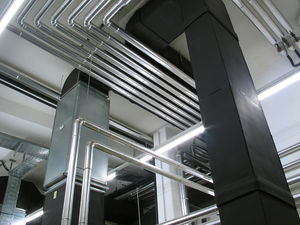
Don’t SHOCK the Boiler
During our design review of a recent project using closed-loop ground source heat pumps, we recognized the possibility for water entering the heating boiler to be well below the minimum entering water temperature prescribed by the boiler manufacturer for a prolonged period of time. At our suggestion, the engineer modified the sequences and piping to add a 3-way valve off the boiler discharge to allow it to mix with the return. This valve was intended to modulate to maintain the entering water temperature at 80 degrees F. The engineer issued an addendum with the modified piping and revised controls; the mechanical contractor installed the second valve but the controls contractor never got the addendum. His programming did not initially include the minimum entering water logic. We discovered this during testing and the reprogramming, uploading and testing of to make the correction will take less than 30 minutes. Had the system remained without that logic, the boiler warranty would have been voided and there is a possibility the boiler would have physically failed.
Conclusion
None of us is going to change the pace of construction; HVAC controls will, for the foreseeable future, always be crammed into the final hours of a project. Above are just a few examples of things that are quick and easy to fix, yet could have had major impacts on building operation. These were all caught before they became issues because of a thorough, rigorous testing protocol.
If you are a building owner or construction manager I suggest hiring someone with the right experience to perform thorough functional testing of the HVAC controls prior to occupancy or as soon as possible thereafter. The monetary investment will be minimal overall. In the three examples above, that investment would be paid for many times over simply by recognizing and correcting those errors before they became reality.
