Outside air economizers are one of the most cost-effective, common, promising and troubled energy efficiency components you can find on a commercial air handling system. The concept is simple and beautiful – use outside air instead of expensive mechanical cooling when possible. When outside air is at the right temperature and humidity levels, turn off chillers, cooling towers and pumps, and bring in free air. In reality, however, while our firm has commissioned hundreds of outside air economizers (new construction and retrocommissioning projects), more than 50% of them have not functioned properly, causing significant energy penalties to the building operating costs.
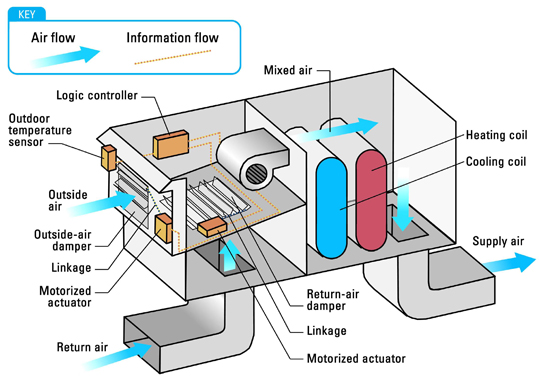
How an Outside Air Economizer Is Supposed to Work
Most commercial and industrial buildings require mechanical cooling throughout the year, no matter where they are geographically located. As conditioning outside air is very expensive, HVAC systems are typically designed to add the minimum outside air volume necessary to meet ventilation requirements. The rest of the conditioned air is made up of return air coming from the building at a relatively neutral temperature and humidity (say 74F and 40% relative humidity). But why mix return air with a small percentage of outside air, if the outside air is of the same temperature to which we are cooling (for example 55F)? It only makes sense that we open up the outside air damper, exhaust more return building air and reduce the load on the cooling equipment. Especially in the northern climates, outside air temperatures can be favorable for a significant portion of the year (in Vermont this is approximately 20% of the year). The following graph is an example of an air handling unit we metered to determine the impact of an economizer. Note the average amperage of the unit went from 18amps to less than 5amps. Over the many hours per year when the outside air temperatures are between 50F and 65F, this can add up!
Are Outside Air Economizers Too Good to be True?
The problem with this great energy saving component is that, in real life, it is hardly ever set up or maintained correctly and the problems it causes can produce great energy penalties instead. An integrated economizer (the only type that should be specified) is comprised of the outside air, exhaust air and return air dampers, and temperature and humidity sensors measuring outside air and return air. The dampers are controlled by the unit (if it’s a stand-alone rooftop unit) or building DDC system sensors. The controller analyzes the building return temperature and relative humidity as compared to the outside air temperature and humidity (the combination of which yields the enthalpy of the air). When the outside air conditions result in a lower enthalpy than the return air conditions, the dampers modulate to bring in more outside air and exhaust more return air.
Two common problems we have seen are that damper actuators do not function, so dampers are not responding to the controller, and sensors are out of calibration, even in new construction. These issues cause the dampers to position themselves incorrectly and outside air to be brought in at the wrong times. Even more common, unfortunately, is that the controls are typically not programmed correctly. As an example of what trouble this causes, picture a hot day of 87F and 90% relative humidity and the outside air damper is stuck or programmed to be fully ‘open’. No design engineer has sized the HVAC equipment to be able to handle such a large cooling load and the building will overheat significantly, and we end up with lots of occupant complaints. Problems like these lead to unnecessary expenses such as equipment replacements, equipment oversizing, loss of tenants, and higher energy costs. The solutions, on the other hand, are quite simple: due diligence in installation and control setup, and annual maintenance. It’s worth it!
