During this recent cold-snap in the northeast (where it reached -20F at my house in Montpelier one morning!) you can be sure that HVAC contractors were some of the busiest people around. Inevitably, when outdoor temperatures reach what are called “design-day” conditions, (the days with the highest expected heating or cooling loads a building can experience for its local climatic conditions), HVAC systems are put to the test. It is not uncommon for problems that are not obvious at lower temperatures to suddenly arise-- sometimes leading to system outages, frozen pipes, and worse---exactly when you need your HVAC system the most.
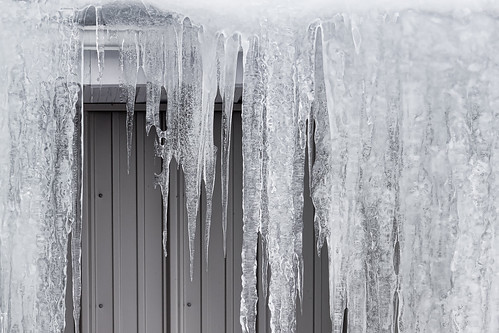
Engineers to the Rescue
As consulting engineers, we often get calls during periods of extreme weather to help troubleshoot problems that arise in existing buildings, and to identify solutions. And as commissioning authorities, when working on new buildings or optimizing existing buildings, we do all we can to identify potential issues ahead of time so that these kinds of seasonal extreme, weather-related problems don’t surface down the road for the building owners we work for.
Functional Performance Testing
An essential part of the commissioning process--functional performance testing--is typically performed in large part near the time of the project completion. During this process, the controls and programming are put through their paces to verify that they work as designed, but also in a manner that will be reliable and provide the highest degree of energy efficiency. While many of the weather conditions for an entire year can be “simulated” to verify the system is operational at the initial testing, some aspects cannot be reliably tested without the actual weather conditions present. Opposite Season Testing (as the reader might guess) is a continuation of HVAC functional performance testing during the season opposite the original testing. So if the cooling season in dominant at the time of project completion and initial functional testing, additional testing will be scheduled during winter months.

An Example of Opposite Season Testing
As an example of the value of opposite season testing, during a project Cx Associates had at a local college, an air handler was programmed with a sequence which, during startup from the unit being offline, opened an outside air damper too quickly--allowing freezing air to flood into the mixed air box resulting in tripping of the preheat coil protection freezestat (a low temperature limit safety device). This issue had not been clearly identified during the initial summer testing period, but during opposite season testing, was discovered tripping repeatedly whenever restarted during below freezing weather. By performing opposite season testing early on, we were able to identify this issue prior to it ever being a nuisance or alarm issue for the owner.
Plan Now to Avoid Problems Later
So, whether you’re commissioning a huge new building or doing a small controls upgrade project on an existing building--have the HVAC system tested as thoroughly as possible when the project is in initial functional testing, but also consider some rigorous opposite season testing to catch those issues that are harder to identify. Opposite season testing can help to identify issues early on with possibly big savings on maintenance calls and long-term energy costs.