What does sound control have to do with energy efficient design? This blog post is the first in a three part series that will explore the intersection of sound and energy efficiency in existing buildings. My early experience as an applications engineer in mechanical systems noise control made me aware of the connection between the built environment and equipment energy use. System airflow requirements and the impact of total added pressure drop of sound control solutions are primary design variables for a noise control engineer. Full scale HVAC aero-acoustic laboratory testing is an integral component of sound control design.
Importance of Sound
The sound environment in buildings is a comfort condition which significantly affects productivity, occupant satisfaction, and our ability to learn. Any design engineer involved in large-scale building projects has had to consider the impact and control of sound. For a building design to be successful, the built environment, including the background sound level, must be usable for its intended purpose. Since air is widely used for heat exchange and ventilation in HVAC design, and air delivered to a space will convey the sound created by the mechanical equipment and duct system components that it encounters, reduction and control of aerodynamic sound has a reciprocal impact on the design and operation of airside mechanical systems.
Good Design
A good design serves the full range of operational requirements at the lowest possible energy and financial cost over the life of the system. Noise is wasted energy. If a system is noisy, energy is probably being wasted. To give an example of where an improvement in energy efficiency also resulted in mitigation of noise, in a recent pro bono design review by Tom Anderson of Cx Associates for a local church, an oversized air handling unit was eliminated in favor of a smaller energy recovery unit. The result was a smaller, quieter, less expensive system that could be located in the basement away from a noise sensitive sanctuary, easily meeting the stringent NC-20 acoustical design target. Thus a good design was reached through control of energy and noise.
Opportunities in Retrocommissioning (RCx): What to Look For
How can you make low cost modifications to airside distribution systems that will improve occupant comfort and reduce energy costs? From a noise/energy control standpoint, it is generally effective to start at the source, for example, by reducing fan speed, lubricating bearings, and making sure belts are properly tensioned. Even if your building does not currently have variable speed fans or a sophisticated building management system, significant annual savings from improved air distribution design may still be a low cost opportunity.
Reducing unnecessary static pressure losses (such as “system effects”) in an existing constant volume system can improve opportunities for lower fan turndown resulting in quieter sound levels and lower energy use.
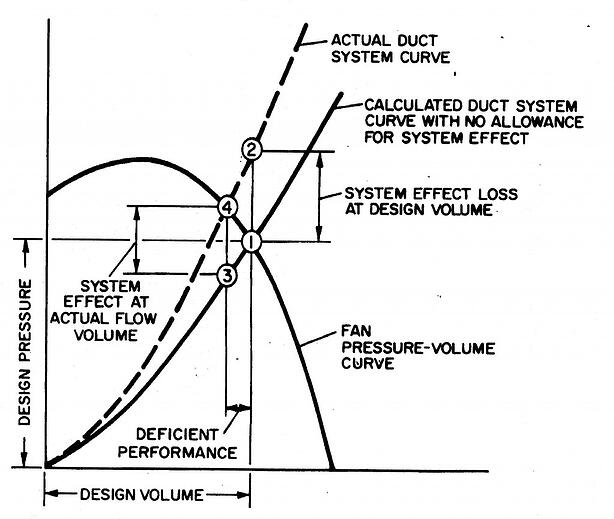
If a system is noisy, it should be on the top of the list for a review of energy efficiency measures, but even if noise is not excessive, there may still be unnecessary losses associated with construction and balancing of your existing systems. Did the balancer add system pressure drop by closing dampers to meet the engineer’s specified operating point, instead of reducing fan speed? If so, the system could be rebalanced for lower fan speed by opening dampers and installing a VFD or resheaving the fan. Did the HVAC contractor install an abrupt transition immediately after the fan? Alternative routing or fan reorientation will mitigate high head losses in blast areas.
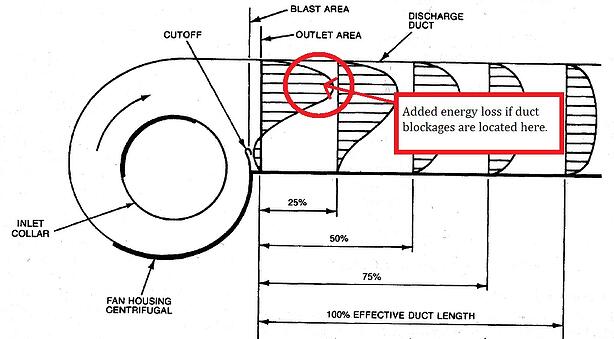
In another example, a standard sound attenuator may already be installed, adding 0.25” w.c. static pressure drop to the system, permanently, at all times. If such an attenuator is installed in a non-ideal location due to difficult site conditions, this pressure loss could increase by a factor of two or more due to airflow turbulence interactive ‘system’ effects [1].
It may be possible to replace the sound attenuator for a few hundred dollars with one that adds no pressure drop, or to relocate it to a more favorable location. Potential annual cost savings for eliminating 25% of system pressure drop for an existing mid size constant volume fan may be comparable to average savings for an existing similarly sized VAV supply system with static pressure reset control, assuming an average CFM load of between 75% and 80% design CFM. While 75% to 80% may be on the high side for a typical VAV system, the potential savings for reduced static pressure on a constant volume fan can be in a similar range, 15,000 to 20,000 kWh ($1,500 to $2,000) per year.
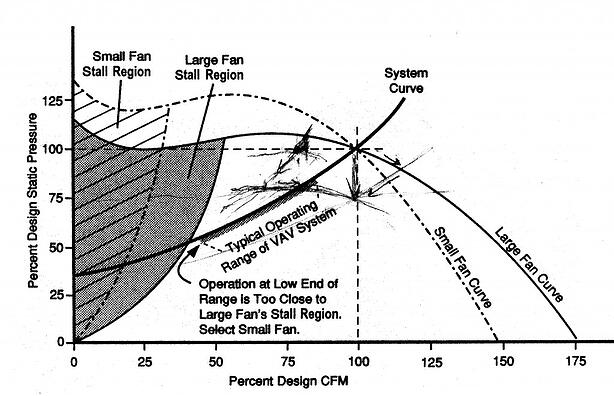
Make the Most of your RCx Investment
In summary, low cost improvements could result in significant energy and cost savings for a mid size constant volume supply fan, typically paying back in less than five years, even for systems without direct digital control.
An awareness of sound control issues and methods can help your existing building RCx project maximize energy and cost savings and occupant comfort. Even if a system is equipped with automatic controls, a walkthrough of the physical systems and a drawings review including air distribution systems are essential before sitting down with the controls contractor to ‘tweak’ the systems. The danger of relying on controls alone to reduce energy before understanding the actual as-built existing systems is that your RCx effort may only scratch the surface of potential savings.
[1] Application of Manufacturer’s Sound Data, ASHRAE, 1998